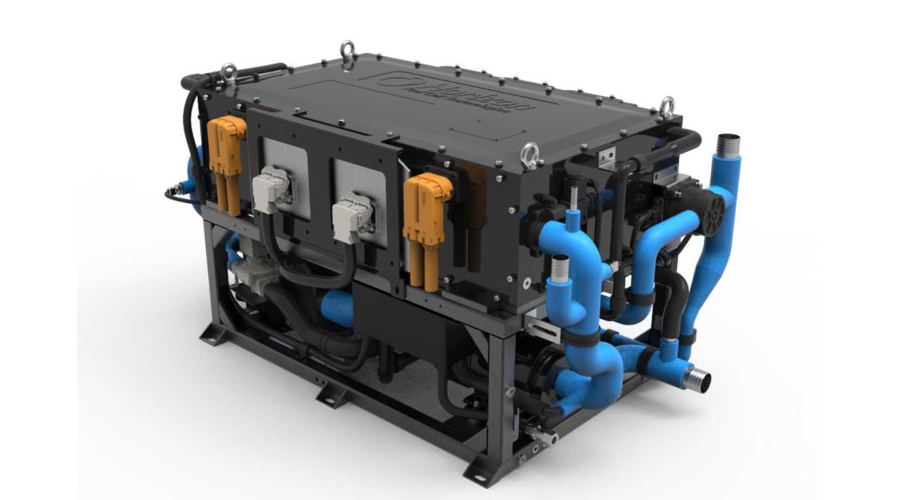
When we talk about the PEMFC (Proton Exchange Membrane Fuel Cells) industry, we clearly have in mind polymer membrane plates and how they work. We think of how electric current is achieved by the passage of electrons through an external system, as the protons pass through the electrolyte, which simultaneously acts as an electrical insulator, proton conductor and separator of the reactions taking place at the cathode and anode.
However, this reaction is determined by many factors that will influence it. Polymer Electrolyte Membrane Fuel Cells (also PEMFC) are extremely sensitive systems. The industry will require a great deal of investment in R&D and refinement in the production and supply chains of many downstream industries to achieve the optimization and democratization of PEMFC engines.
There are many secondary components that need to advance and develop in parallel: compressors, valves, catalysts, electrolytes… and the hoses.
Gases and fluids in PEMFC systems
In a Proton Exchange Membrane Fuel Cells system there are 3 gas or fluid conduction subsystems:
- Anode
- Cathode
- Cooling
Each of these subsystems is specialized in the elements it conducts internally and in the requirements of their respective related systems. In the case of PEMFCs these requirements are significantly high.
Requirements:
- Permeability: hydrogen is a highly flammable gas (and also a high value product) and therefore the tightness of the system is a critical safety requirement.
- Purity: As is well known, these batteries are highly sensitive to possible external contamination which can lead to a significant and rapid reduction in engine efficiency. This factor depends on 2 determining agents:
- External contaminants adhered to the tube that can be detached when the system comes into operation.
- Internal contaminants: material in the pipe or connections, including any chemical compound or inorganic element, that can be detached during system operation.
- Conductivity: the electrical conductivity of the materials carrying the various gases or fluids will be critical in determining the safety of the system.
Permeability is usually a requirement unique to the Anode, while purity and conductivity usually impact all three subsystems.
Materials that offer a solution:
In the experimentation and prototyping phase that this industry went through until 2015, basically inflexible materials were used (such as Stainless Steel or Aluminium pipes) that provided more security with respect to the permeability of the system to the detriment of flexibility.
But, given the increasing development of the industry, new materials and components are required to suit the feasibility of these engines for use in vehicles and for mass production.Â
To put it simply: the PEMFC industry needs flexible pipes.
Flexible hoses for PEMFC motors
The challenge lies in how to meet the 3 critical requirements of these engines, using elastomers.
Let’s remember: permeability, purity, and conductivity.
But other general industry requirements must also be met: temperature (depending on the type of PEMFC LT or HT), pressure, flexibility, weight…
Materials for anode and cathode tubes:
FKM
The most popular choice now to overcome these high requirements is FKM (Fluorocarbon-based Fluoroelastomer material). A material with a very low permeability compared to other elastomers, with a significantly high internal purity level and relatively good chemical compatibility.
EPDM-based hybrid
On the other hand, a material created and popularized by the company Venair, called Vena® PEM CELL, is also becoming known. It is a specially formulated EPDM that the company has created to specifically meet the 3 basic requirements of the sector.
According to the company: “We already have more than 25 OEMs around the world using Vena PEM CELL in their prototype and series production in the Anode and Cathode as well as in the Cooling system”.
Silicone
When talking exclusively about the cathode, some companies choose silicone as the material to conduct the Oxygen. Silicone tubing would not be suitable for the anode because of its relatively high permeability, but it can be used for the cathode if a high purity silicone is chosen to minimize the level of particles (leachable) extracted from the material during the operation of the system.
Materials for the cooling system:
This high purity silicone is always recommended for the cooling system. Since PEMFCs have very high purity requirements, experts recommend using high-purity silicone for cooling as well. This ensures the minimization of leachables extracted from the material while the motor is running.
Some companies continue to use conventional silicone (peroxide cured silicone) in cooling systems. This option is riskier in terms of membrane contamination, but if the tube has followed a very strict production and cleaning protocol to ensure the minimum amount of internal and external contaminants, it can be used.
PEMFC Tube Suppliers
Analysing the sector, we can find some companies that are approaching on PEMFC tubes but very few are getting good results, probably because of the difficulty to meet all these requirements:
- Specialty in FKM (difficult material to work with)
- Specialty in ultrapure products (biopharmaceutical level)
- Working with purity and high cleanliness levels comparable to the biotech sector
- Optimized supply and production chain to absorb such a susceptible industry
- Enormous investment in R&D (innovations in materials, purification processes, supply chain…)
- Having a large quality department to detect minute imperfections
The most specialized and focused company we have found dedicated to this sector, as mentioned above, is Venair.Â
Venair, dedicated to the production of industrial and biopharmaceutical tubing using elastomers, began specializing in the PEMFC industry about 10 years ago. “We knew it was the future of mobility and that by 2020 all major vehicle manufacturing companies would be developing and selling Fuel Cell Electric Vehicles (FCEV)” says Marc Balcells, Fuel Cells Project Manager of Venair.
Venair has invested years researching materials and certifying its hoses to meet all industry requirements. As they tell us, they have more than 25 years of experience with FKM tubes and shapes, their 2 most powerful businesses are the Biopharma and PEMFC sectors.Â
Today they already have certifications for their FKM and ultra-pure silicone constructions for industries such as railways (EN-45545-2) or flammability certifications (UL 94). They are also in the process of becoming the first company in the world to obtain Fuel Cell Hoses for Marine Industry certification (DNV certifying entity).
The company already supplies more than 90% of the major manufacturers of Polymer Electrolyte Membrane Fuel Cells in Europe, America and Australia. And they are already starting to enter the Asian markets.
With this level of experience and investment in quality and R&D, for the moment they are the leading company in the PEMFC tube industry.
Sponsored Content: Venair
Read the most up to date Fuel Cell and Hydrogen Industry news at FuelCellsWorks