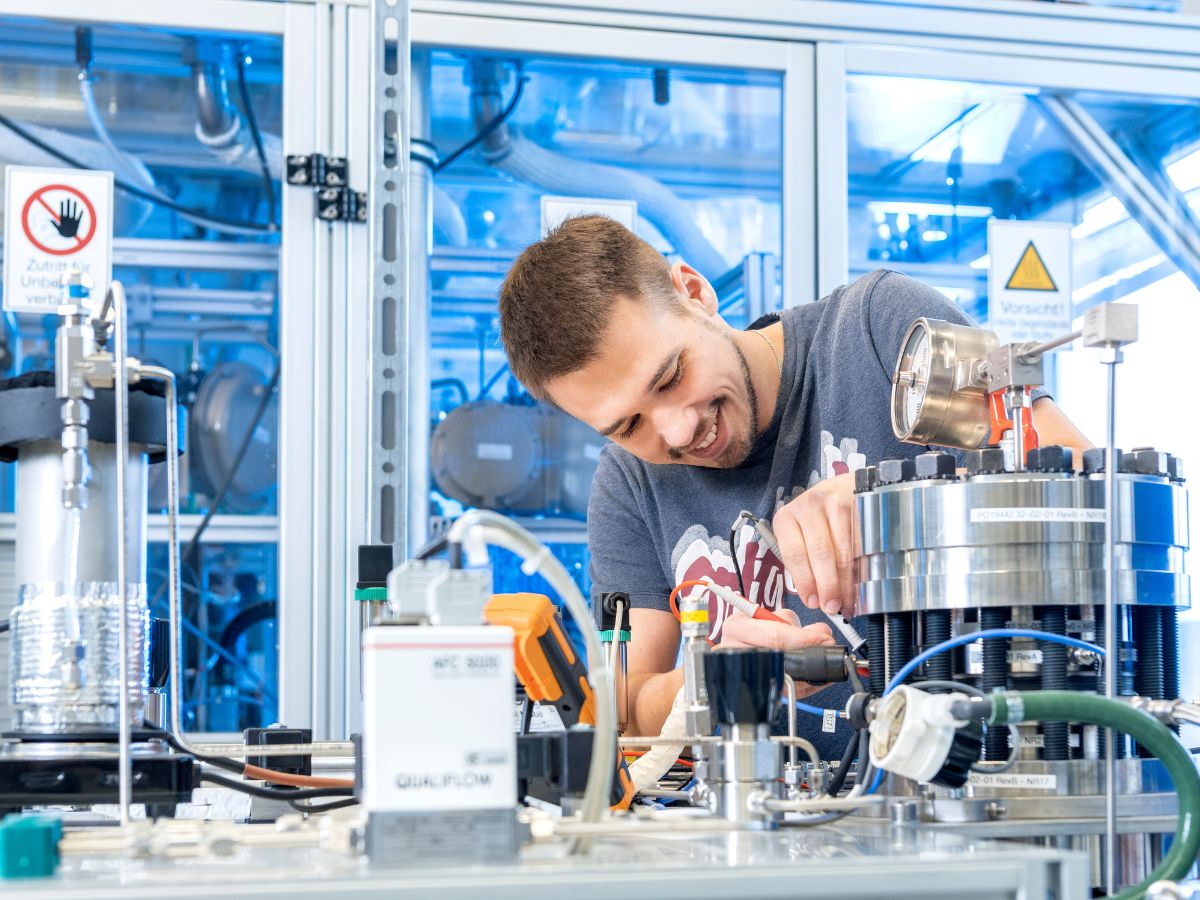
Recycling instead of producing anew—this is also possible with hydrogen, saving electricity, money, and CO2 emissions. Under what conditions and with what economic potential for the industry, the EH2C project team led by Prof. Dr. Sven Schmitz of the Baden-Wuerttemberg Cooperative State University (DHBW) Mannheim found out. The team, together with five project partners, focused on semiconductor manufacturing. The results for hydrogen recycling are so convincing that they can also be an important decision criterion for other industrial sectors to switch to hydrogen technologies.
Hydrogen is used in various industrial processes without being consumed, such as in solar cell and semiconductor production: the used hydrogen is purified from environmentally harmful substances and then mostly released into the environment without any utilization. Resources are wasted because producing the promising energy carrier anew requires new electricity. Therefore, a team from the Electrochemistry Research Cluster (ELCH) at DHBW Mannheim dedicated themselves to demonstrating electrochemical compression as an innovative technology for hydrogen recycling in semiconductor manufacturing in the EH2C project.
Resource-efficient, economical, and top-quality:
Cleaning and compressing hydrogen using EHC
For valid insights, the project partner centrotherm clean solutions GmbH in Blaubeuren built and certified a complete cleaning system with an electrochemical compressor (EHC) as its core, which was then tested at the project partner Fraunhofer ISE in Freiburg. The recycled hydrogen from this system was then tested for two different semiconductor manufacturing processes: silicon carbide production and metalorganic vapor phase epitaxy. The results were among the highlights of the research project: whether the production was done with new or recycled hydrogen made no difference in the quality of the manufactured semiconductors. “With this method, we offer the industry a very attractive alternative because there are no quality losses with recycled hydrogen—and that is the most important aspect for manufacturers. But it is also economically and ecologically convincing: when hydrogen is recycled with green electricity, we save about 80 percent of the green electricity that would otherwise be necessary for the electrolysis-based production of hydrogen,” says project leader Prof. Dr. Sven Schmitz, pleased with the project’s results.
Important step towards decarbonizing industry
Another advantage of the EHC and thus the entire recycling process: it is easily scalable in size, so it can clean very small (hydrogen flow approximately 1 kg/day) as well as very large exhaust streams (hydrogen flow up to 100 kg/day). An electrochemical compressor with a size of 5.5 kg/day was tested. Depending on this, the total costs vary: for a large EHC with high efficiency, the initial investment is high, but the operating costs are low—while for a small EHC with low efficiency, low initial investment and high operating costs can be expected. However, there is also positive news regarding the investment costs from the EH2C team: “In the future, the investment in an EHC could become significantly cheaper since it can be manufactured on the same machines with the same basic materials as electrolyzers producing hydrogen and fuel cells consuming hydrogen, both of which are expected to have high production volumes,” says Prof. Schmitz.
“Functional H2 recycling facilitates the transition to H2 in industry”
Because the results were so positive, a follow-up project with the partner centrotherm clean solutions GmbH is already in planning. In this project, the cleaning system will be scaled to 30 kg/day, corresponding to a size needed in a real semiconductor factory. With 30 such systems, a factory could save up to 30 barrels of gasoline per day, including the associated CO2 emissions. “Since 2015, we have been working with centrotherm clean solutions GmbH. From a very small scale in the laboratory to actual product development, we have realized several projects together on the way to successful hydrogen recycling. Milestones like those from EH2C will also make it easier for other industrial sectors to switch to hydrogen technologies,” Prof. Schmitz is confident. Another example from DHBW ranks for valuable application-oriented research and successful transfer between science and practice.
Together for a sustainable industry
The EH2C project was funded by the Federal Ministry for Economic Affairs and Energy (BMWi) for 2.5 years as part of the 7th Energy Research Program of the Federal Government and has been completed since December 31, 2023. The project team at DHBW Mannheim included Prof. Dr. Sven Schmitz as well as the scientific employees Christian Geml and Kai Tornow. During the project, they focused on gas analysis, i.e., the quality determination of hydrogen, the analysis of all energy flows, and the testing of the service life of the EHC when exposed to particularly critical gas components.
External project partners were:
- centrotherm clean solutions GmbH, Blaubeuren (Lead coordination)
- Fraunhofer Institute for Solar Energy Systems ISE, Freiburg
- FCT Systems GmbH, Frankenblick
- AZUR SPACE Solar Power GmbH, Heilbronn
- HyET Hydrogen B.V., Arnhem/NL (Associated partner)
Main Image caption: One of the experts working with an Electrochemical Compressor at DHBW Mannheim: EH2C project employee Kai Tornow in the Eppelheim Hydrogen and Fuel Cell Laboratory. (Copyright: Rhine-Neckar Metropolitan Region)
Read the most up to date Fuel Cell and Hydrogen Industry news at FuelCellsWorks