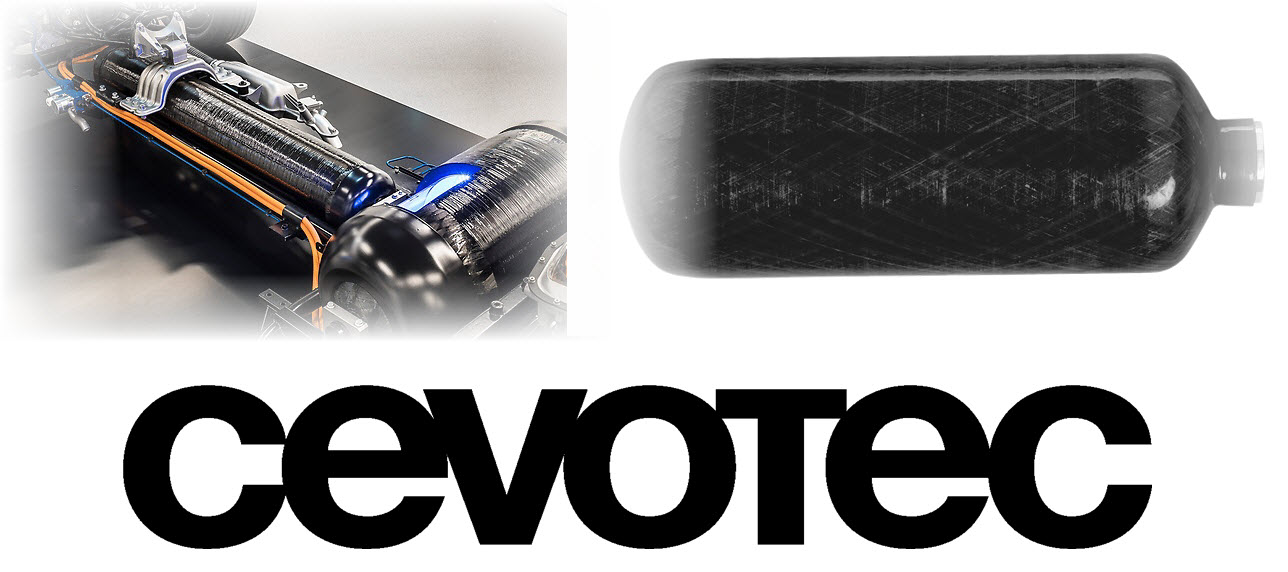
- High pressure with ease in hydrogen-powered vehicles
Hydrogen-powered fuel cell electric vehicles (FCEV) are superior to battery-powered cars in several ways. Refueled in just a few minutes, they have a longer range and still offer all the performance advantages of the electric motor. But the technology is still young and needs to overcome some challenges.
From the standpoint of the composite industry, in particular, the significant amount of fiber material needed to make the hydrogen tanks stands out. Cevotec’s engineers took up this challenge and developed a solution that saves 20% in time, material and cost in the production of composite-based pressure tanks.
“The automotive industry has invested billions in the development of fuel cell technology, but currently very few such vehicles are on our roads. One of the problems is the efficient and safe storage of hydrogen in the vehicle, “says Thorsten Groene, CEO of the Munich-based fiber patch placement specialist Cevotec. “In the tanks, there is a working pressure of up to 700 bar, which means about 10 kg of carbon fiber for 1 kg of hydrogen storage – that’s a lot.”
Accordingly, manufacturers are keen to process less of the expensive fibers to reduce the weight and cost of the tanks. “Wrapping continuous filaments around a core is the best way to produce the cylindrical part,” says Dr. Neven Majic, Executive VP of Cevotec. “But such a direct filament deposit on the domes means redundant material on the cylindrical part – which greatly increases the weight and cost of the final product.” Cevotec’s solution is to incorporate carbon fiber patches of the same material before the winding process in the dome areas. “The patches are designed to cover exactly the areas that cause winding problems,” explains Majic. In a first process step, coupling of the tank core is reinforced with patches,
“The investment in the patch technology pays off from the very first day of production,” says Gröne. A single FPP system can provide pressure tanks for multiple winders with patch reinforcements. Manufacturers can achieve at least 20% savings in material and cycle time. “When winding and patch technology are combined in series production, the FPP investment already pays for itself within the first year. It’s a pretty simple calculation that we can present to our interested customers. “
By consistently applying Fiber Patch Placement technology to today’s composite component manufacturing challenges, Cevotec is supporting the development of composites for a green mobility revolution. Manufacturers switching from manual production to Fiber Patch Placement benefit from material efficiency and cost savings of 20% – 60%.
About Cevotec:
Cevotec enables manufacturers to produce complex fiber composite components in high volumes and quality – through intelligent process automation based on Fiber Patch Placement technology. With SAMBA Series, Cevotec offers an individually configurable automation platform for automated fiber deposition that is particularly suitable for demanding 3D geometries and multi-material laminates with complex fiber architecture. ARTIST STUDIO is the associated CAE software for laminating and automated robot programming. In addition to development services that include FE-based modeling and simulation, Cevotec offers the complete process chain from digital design to the finished fiber device.
Read the most up to date Fuel Cell and Hydrogen Industry news at FuelCellsWorks