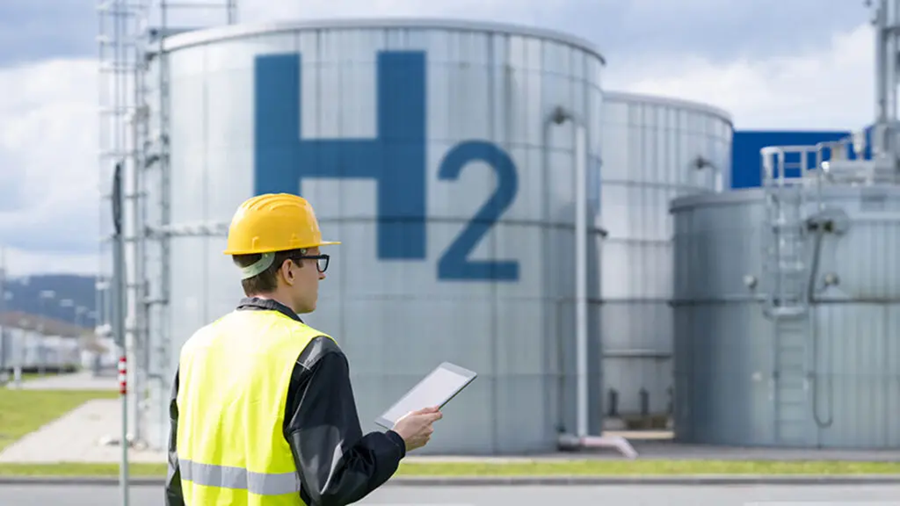
Hydrogen is projected to be a major source of clean energy that would be an integral part of energies and chemicals companies’ net-zero strategy, increasing the need for hydrogen safety processes, systems, and best practices.
Hydrogen is a transportable energy carrier and has high energy potential that can be used as fuel for transportation, power generation, heating, and industrial applications. Unlike natural gas, hydrogen produces clean combustion without greenhouse gas emissions. However, from a fire and explosion-hazardous point of view, hydrogen is less safe than natural gas because it can ignite more easily. It has a lower ignition energy level, a wider range of flammable concentrations, is more prone to leaking, has no smell, burns hotter than natural gas, and can produce higher overpressure and explosion. A wider range of flammable concentrations and quick flame speed implies hydrogen combustions are more difficult to control. Hydrogen has a higher heating value per pound, but it will require a much higher volume to generate the same amount of energy as natural gas. Below is a table that shows the physical properties between hydrogen, methane/natural gas, and petrol/gasoline.

The Bureau for Analysis of Industrial Risk and Pollution (BARPI) ARIA database report provided an analysis of 215 industrial hydrogen-related accidents worldwide. The majority (60%-70%) of these hydrogen accidents occurred in the energies and chemicals industry. It is not clear what percentage of this data is related to green hydrogen production, but the numbers are most likely small since the accident data was compiled before 2007. An interesting observation of the statistic is that 70% of the accidents resulted from “organizational and human failure”, hence the prevention should focus on hydrogen risk awareness and company safety procedures. Having said that, since more than 90% of the hydrogen produced today is from fossil fuels and used primarily in refining and fertilizer industries, the standard industry practices and regulations require high availability of functional safety systems to be installed for process safety.

Green Hydrogen Electrolyzer
The basic concept behind green hydrogen production is the electrolysis process using electrification to break water molecules into hydrogen and oxygen. The electricity must be sourced from renewable power for it to be called green hydrogen. A typical green hydrogen plant operates on a 5-25 MW electrolyzer, but we are seeing bigger plant capacities with upward of 100 MW being planned.
Increase Electrification and Scaling up Production Capacity
The challenge for green hydrogen production, especially if it is integrated into chemical, refinery, or petrochemical plants, is not safety, it is the scaling up of production capacity and the electrification process. Industrial safety standards such as Occupational Safety and Health Administration (OSHA), Process Safety Management, ISO, NFPA, IEC, etc. already include flammable gas like hydrogen. Hydrogen is typically produced using a thermochemical process called steam reforming. It is often referred to as gray hydrogen. This process is similar to other thermochemical processes within the plant, so it is integrated into plant safety. For example, in a refinery, a large amount of gray hydrogen is produced and utilized in the hydrodesulfurization process and hydrocracking process. Blue hydrogen that depends on CCUS to decarbonize the grey hydrogen does not change the safety protocol within these plants either. Green hydrogen that is based on an electrification process is different from thermochemical processes—a process not familiar to traditional chemical and refinery and petrochemical operations. For example, for a typical refinery of150,000 bbl/d, the electrolyzers that replace the steam methane reformer require an additional 100 MW grid power to generate green hydrogen; this is almost 200% more than the traditional grid power required for an entire refinery of this capacity. For standalone green hydrogen producers, the scale of production will have similar challenges scaling up from 25 MW to 100 MW. Rectifier control and higher power load require larger electrical infrastructure and electrical safety measures. Incorporating renewable electrical power sources with traditional fossil fuel power to produce hydrogen can be a transitional or hybrid process that requires microgrid optimization. Combined power and process safety is becoming more critical from a lifecycle standpoint, including design, engineering, operation, and maintenance.
Hydrogen Safety Standards
There are several existing industry standards that are related to hydrogen:
- ISO 198880-1:2019. The standard provides safety requirements for hydrogen generators that use a water electrolysis process for industrial applications.
- NFPA 2: Hydrogen Technologies Code. The National Fire Protection Association (NFPA) developed this code to address the safe installation, storage, use, and handling of hydrogen in various applications. It covers aspects such as hydrogen generation, storage, transportation, and utilization.
- IEC 61508: Framework to ensure the functional safety of electrical/electronic/ programmable related systems in various industries, including hydrogen.
- ISO 14687. Product specification for hydrogen fuel, including purity levels limits and other aspects. Ensuring high-quality hydrogen is crucial for safe and efficient utilization
- ASME BPVC Section VIII, Div. 1. A boiler and pressure vessel code that covers the design, fabrication, and inspection of pressure vessels. It includes requirements for hydrogen storage tanks and pressure vessels.
- IEC 62282 Fuel cell technologies. This standard covers various aspects of fuel cell technologies, including safety.
Hydrogen gas pipelines are operating under higher pressure which can cause embrittlement, small cracks, and dents in older pipelines, creating leakage and ruptures. The general guidelines and research so far are that an existing gas pipeline can handle up to 20% hydrogen blends. Materials such as steel alloys, composite materials, and specialty polymers are commonly used for hydrogen storage and transportation. An adequate leak detection system and proper ventilation system should be installed in the storage area to prevent combustion. Conversion from hydrogen to ammonia and methanol is considered a good energy carrier for easy voluminous liquid transport. Some of the standards for hydrogen and ammonia transportation can be outdated and not made for large scale. Using hydrogen as a fuel in hydrocarbon processing can be a challenge because hydrogen burns hotter than natural gas, special consideration must be given to the metal selection.
Integrating Electrical Safety with Process Safety
Hydrogen applications are nothing new in the energy and chemicals segment. Green hydrogen electrification will be a part of the risk assessments included in the HAZOP (Hazard and Operability study). Safety experts need to reevaluate electric risks and conduct an electrical HAZOP. New safety concerns include overheating of cables that can lead to an electrical shutdown or an arc flash. Process safety and electrical safety need to be combined as the process becomes more electro-intensive. Electricity supply is key for green hydrogen because it represents around 70%-80% of the total cost of generating green hydrogen. Substantially higher electrical loads and electrical infrastructure unforeseen by hydrogen production are creating newer safety concerns. Digitalization enabled by IT/OT convergence demands tighter cybersecurity protocols. Cybersecurity strategies should be included in process safety best practices because cybersecurity is essentially digital safety and a key component to protecting the uptime, security, and safety of critical infrastructure.
Process Safety Best Practices for Hydrogen Production
Properly Designed – Process designs should incorporate hydrogen safety standards and protocols from HAZOP, PHA, LOPA, and SIL/SIF studies. Developing a digital twin of the hydrogen plant and its assets will impact the plant’s safety throughout its lifecycle. For example, dynamic simulation and operator training based on digital twins train operators to handle abnormal hazard situations. Incorporating cybersecurity IEC 62443 design practice into IT and OT.
Well Built – Integrated control and safety system automates the process and provides the most effective prevention against abnormal situations. It is important to incorporate cybersecurity IEC 62443 design into IT/OT interconnection, device hardening, remote access points, and firewalls. Ensure proper ventilation in areas where hydrogen is produced or stored to prevent the accumulation of hydrogen gas. Install hydrogen gas detectors and monitoring systems to detect leaks or abnormal gas concentrations promptly. Regularly calibrate and maintain these monitoring systems.
Safely Operated – As operations change dynamically, processes, people, and technology need to evolve as well. An alarm management solution prioritizes alarms and resolves alarm flooding issues. Safety data analytics systems monitor and review safety workflows, making recommendations to repair or modification. Operator Training Systems and Augmented Reality software solutions ensure operator skills are updated. Remote operations to improve worker safety is enabled by digitalization technologies like cloud and advanced analytics. Cybersecurity detection, awareness, and training will ensure safe operations.
Properly Inspected – Procedural automation and mobile operator rounds ensure assets are performing reliably and safety procedures are followed. Cybersecurity is on top of the mind of most CIOs, and cybersecurity audits can be a good starting point.
Well Maintained – Control systems modernization is considered when the system is aging and reliability becomes an issue. Asset performance management solutions ensure the asset reliability of instrument devices, valves, compressors, and pumps. Cybersecurity response recovery procedures and software patch management are essential parts of the maintenance. Adequate personal safety measures like PPE, fall protection, and access security protects workers from injuries and sickness.
Integrating electrical safety with process safety will be essential as electrification ramps up. The most effective electrical safety strategy is prevention. The goal is to protect people & prevent fire.
Electrical Safety Best Practices for Hydrogen Production
Properly Designed – Review electrical system design with power system experts during the design phase.
Well Built – Incorporating standard built-in design power systems like MV switchboards, LV circuit breakers, and motor control centers guard against electrical hazards. Consider additional innovative solutions like Arc Flash detection, wireless self-powered thermal monitoring, enclosure-based arc resistance, onboard racking, remote racking, and remote controlling.
Safely Operated – Ensure adequate electrical safety training of an operation with haptic virtual reality solutions
Properly Inspected – Audit electrical systems with the Modernization, Performance, Safety (MPS) Enterprise Study and an Arc Flash Study
Well Maintained – Safely maintain, connect, and monitor electrical assets with remote analytics and expert diagnostics.
Safety will always remain the top priority for energies and chemicals companies, and safety will evolve with the rise of the hydrogen economy. As a global specialist in energy management, industrial automation, and digitalization, Schneider Electric can play a relevant role in helping clients with green hydrogen design, engineering, operations, and maintenance to be safer, more efficient, reliable, and cost-effective.
SOURCE: Schneider Electric Blog
Read the most up to date Fuel Cell and Hydrogen Industry news at FuelCellsWorks