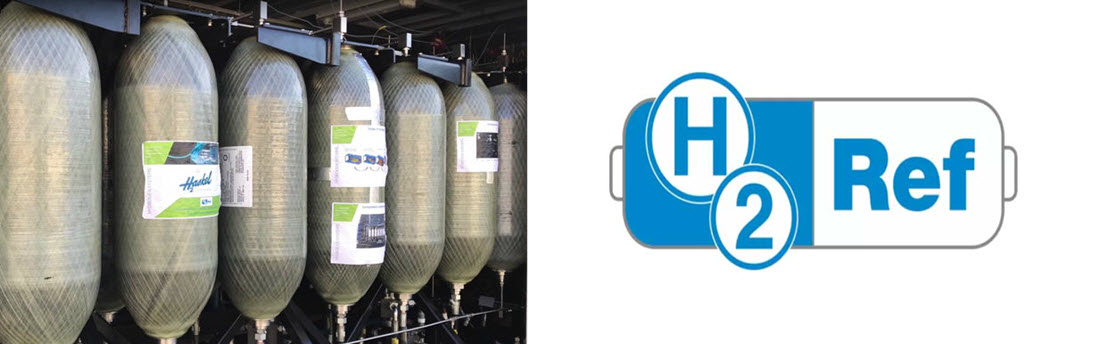
- H2REF – Advanced new compression and buffering solution for hydrogen refueling stations
Recently, the results of the H2REF project , including the main findings, have been presented.
The project aimed to develop an advanced new compression and buffering solution for hydrogen refueling stations (HRS) of 70 MPa passenger FC-vehicles. This solution is based on the use of hydro-pneumatic accumulators, which provides a more reliable and economical solution while improving performance. The project was developed by a consortium of six partners from European countries (France, Germany, Norway and the United Kingdom) bringing together the key experience, knowledge base and resources for reaching the objectives of the project.
According to the various project partners, the system would reduce investment costs by 40% compared to a “conventional” hydrogen refueling station. Which solves the delicate economic equation related to the deployment of stations.
Results
First of a kind high-pressure bladder accumulators in composite material, for operation at up to 90 MPa with demonstrated lifetime.
The H2Ref consortium is composed of six partners from four European countries (France, Germany, Norway, and United Kingdom) bringing together the key experience, knowledge base and resources necessary for reaching the objectives of the project with the work-plan proposed.
The focus from the two main industrial partners Haskel and Hexagon are in the continued development of this compression technology, with the view of eventually jointly developing a highly competitive Compression and Buffering Module (CBM) product offer. This aim certainly has the potential of a major commercial breakthrough if the project results are achieved. H2Nova , as developer and owner of intellectual property and CCSwith expertise in RCS development and compliance, are also interested in such a development. Cetim and LBST will support the consortium with their wealth of knowledge of experience in this particular field of development.
The basic concept
Bladder accumulator-based compression is applicable to any refueling applications, thanks to the combined high scalability of hydraulics technology and carbon composite pressure vessels. Indeed, high-pressure hydraulic pumps are already available and successfully delivering very large capacities for many oil and gas applications. Similarly, high-pressure accumulators in carbon composite material are also currently available and can be built to very large sizes.
Main advantage of the concept compared to conventional technologies
A fundamental advantage of bladder accumulator-based compression for compression and transfer of hydrogen over conventional mechanical compression, is that it uses serially produced components from a mature and standardized industry (hydraulics and composite pressure vessels) with a world-wide supplier base, minimizing cost while providing excellent robustness and reliability.
Other advantages of the concept compared to conventional technologies
Furthermore, bladder accumulator-based compression provides the following additional benefits:
- high scalability, thanks to the combined high scalability of hydraulics and carbon composite pressure vessels;
- high flexibility, thanks to the wide operating pressure ranges of the components;
- high flow-rate and small foot-print: as compression effort is applied by means of a working fluid driven by a hydraulic pump;
- maximized compression capacity, thanks to uniquely taking advantage of varying pressure upstream, while operating at constant power (even though the discharge pressure to suction pressure ratio changes);
- reduced energy consumption, thanks to the exploitation of upstream pressure:
- the average energy consumption is halved as the pressure of the stored hydrogen is fully taken advantage of;
- the on-going adoption of higher storage pressure in the hydrogen supply chain further increases the benefit of taking full advantage of the source storage pressure;
- improved reliability and reduced maintenance requirements, intrinsic to hydraulic power technology;
- exploitation of the full compression power capacity at all times, maximizing effective throughput.
1. What is the expected cycle life of the bladder accumulator?
There are 2 parts to consider in the bladder accumulator cycle life, the Shell and the bladder.
The shell base assumptions are
- Medium pressure – Expectation is over 15-year life – based on 20 cycles per day (based on 365 days), 2 ½ cycles per refuelings = around 275,000 Cycles
- High pressure – Expectation is over 15-year life – based on, 20 cycles per day (based on 365 days), 1 cycles per refuelings = around 110,000 Cycles
- The same bladder is in both the medium and high-pressure vessels.
- The bladder is classed as a consumable part with an expected life of around 2 years (subject to volumetric ratio applied)
- Target – 35,000 cycles– based on 20 cycles per day (based on 365 days), 2 ½ cycles per refuellings = around 36,500 Cycles
2. What happens if there is a bladder failure?
The bladder has been identified as a potential risk in the system and as such mitigating solutions have been put in place.
N.B. It is important to note that if there is a failure in the bladder that because there is balanced pressure on either side of the bladder the oil will not be rushing into the gas side, more that the gas will defuse into the oil, which will be identified on the Hydraulic side via;
- Volumetrically more Oil (i.e oil with gas) will be released than was recorded as being injected
- Pressure increase in the return line
The system has various sensors to detect these issues and immediately and safely stop the system.
3. When do you see this technology commercialized? –
- The project is currently a full-scale prototype and is currently being validated in a relevant industrial environment some we would regard it as being around Technology Readiness Level (TRL) 5.
- The next stage would to increase the operating time and start to demonstrate it in the relevant environment to achieve TRL 7.
- Look at optimizing the current design to focus on the relevant functions including simplifying some of the processes
- This could all be achieved in as little as 3 years time
4. What other application do you see this being useful for?
- This technology is suitable for both constant and intermittent application, therefore we see that this could be extended to all fuelling applications (buses, trains, boats etc) at different pressures and quantities of fuelling.
- There are additional possibilities for the Tube trailer and cylinder bundle filling, downstream of production from something like a PEM electrolyzer, to create a hydrogen network model of refueling and distribution.
5. What are the next steps for the project?
- The next stage would to increase the operating time and start to demonstrate it in the relevant environment to achieve TRL 7.
- Look at optimizing the current design to focus on the relevant functions including simplifying some of the processes
- Review areas for further improvement and cost reductions for a commercial offering.
6. Who do you see taking this type of product to market?
- Clearly the 2 main industrial partners in the consortium (Hexagon and Haskel) can see the benefits in this technology and how it could complement their existing portfolio of products, therefore it would be most like that the industrial partners will be key in taking this to a commercialized product offering.
You can view our H2REF Webinar using the link below
Read the most up to date Fuel Cell and Hydrogen Industry news at FuelCellsWorks