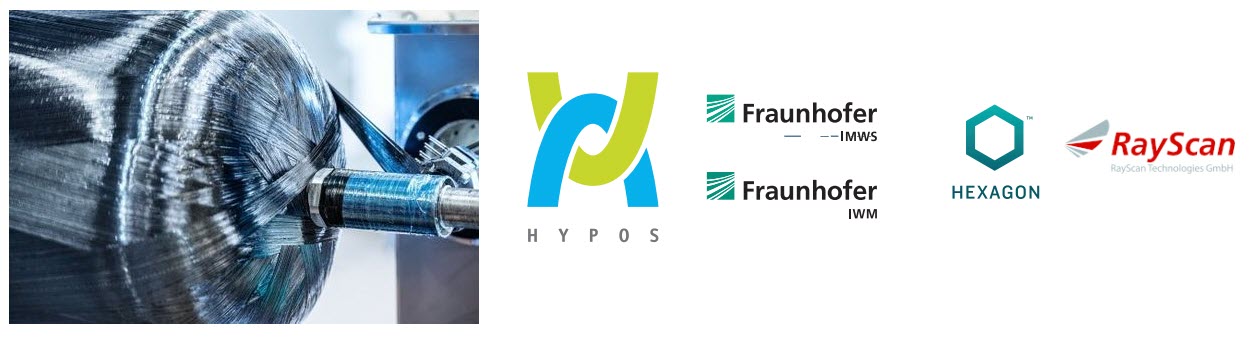
Partners from HYPOS want to enable operating pressures of up to 1000 bar
Green hydrogen plays a key role in the energy transition, as it can be the connecting element between the electricity, mobility and industry sectors. For these potentials to unfold, efficient processes for the storage and transport of green hydrogen are necessary.
The four project partners Hexagon Purus GmbH, RayScan Technologies GmbH, Fraunhofer Institute for Microstructure of Materials and Systems IMWS and Fraunhofer Institute for Mechanics of Materials IWM work together on the development of safe and lightweight high-pressure tanks, in which hydrogen stored at an operating pressure up to 1000 bar and can be transported. This enables a much more efficient distribution and use of this sustainable energy source.
The joint project is part of the HYPOS innovation project, in which more than 100 partners have joined forces to promote the use of green hydrogen in the chemical, refinery, mobility and energy sectors. The starting point for green hydrogen is electricity from renewable energies, which is used for electrolysis, where hydrogen is produced. Thus, green electricity becomes baseloadable and can be used as needed. At the same time, hydrogen is obtained as an important raw material from renewable sources, no longer based on fossil fuels.
Green hydrogen can be stored in bulk storage facilities and transported in pipelines. In order to reach end customers in rural areas or filling stations in the city center and to store them at short notice, appropriate storage and transport tanks are also required. Because gaseous hydrogen has a low volume specific energy density, high pressure tanks provide a viable storage solution: the hydrogen is highly compressed therein. In a tank of the same size, at 1000 bar, almost 600 times more hydrogen than in the uncompressed state and more than twice as much as in a 350-bar container. Although energy is also used for the compression, it is significantly less than, for example, the liquefaction of hydrogen and storage in refrigerated containers at temperatures below -250 ° C.
Common to the market for hydrogen transport are pressure vessels with 200-350 bar, partly 500 bar. The project partners want to significantly increase this value. The aim is to provide particularly safe and lightweight containers that can be used at operating pressures of up to 1000 bar.
“Higher operating pressure offers enormous advantages for efficient distribution and intermediate storage of hydrogen, as well as for efficient tank systems. To achieve this, a coordinated, optimized material and component concept for the pressure vessel is necessary, “says Fabian Richter, development engineer at Hexagon, who coordinates the project, which runs until 30 November 2021.
Particularly suitable for achieving this goal are plastic hybrid tanks. Such containers are encased by a fiber-reinforced plastic as a load-bearing structure. Inside is a thermoplastic plastic liner, which ensures the gas tightness. There are also metal elements at the ends of the container. »This multi-material character brings with it some challenges. The sheathing itself is once again a hybrid of carbon and glass fiber reinforced thermosetting plastics, “explains Richter.
Some problems, such as hydrogen embrittlement or corrosion, are excluded because the liner is not made of a metallic material, but of plastic. There are still some open research questions for operation up to 1000 bar: How does the laminate of fiber-reinforced plastic behave when the tank is filled or emptied? Does the bond between the liner and the jacket remain stable, even with extreme temperature fluctuations and other loads? How does hydrogen interact with the different materials and what effects does this have on their aging and lifetime? How can manufacturing defects (such as ply thickness tolerances, fiber angle deviations, pores, dry fibers) be avoided and how can their impact on the operation of the container be evaluated?
For these questions, the project partners research the fundamentals of materials science. They also want to manufacture and comprehensively characterize scaled model vessel structures and large container models. Last but not least, a suitable test infrastructure for the novel containers should be established in order to be able to demonstrate operational safety with adapted load tests.
In order for the new high-pressure tanks to be able to demonstrate their efficiency, for example, an improved thermoplastic liner material is to be developed and integrated into the container concept, which ensures a low hydrogen permeation rate even at high storage pressures. Based on the material understanding and the microstructure of the materials used, the project partners want to develop a novel macroscopic damage model that can be used for the reliable prediction of component behavior. Numerous, above all non-destructive testing methods are used for this purpose, which are also to be further developed in the course of the project. The goal is concepts for an efficient 3D X-ray examination,
“With safe and lightweight high-pressure tanks, we can combine the ecological potential of green hydrogen with other pluses: to transport the same amount of energy, fewer vehicles or fewer journeys are needed, while at the same time increasing the range of possible applications – and not least, offering considerable cost advantages the companies, “says Richter.
Source: Fraunhofer Institute for Microstructure of Materials and Systems IMWS
Read the most up to date Fuel Cell and Hydrogen Industry news at FuelCellsWorks