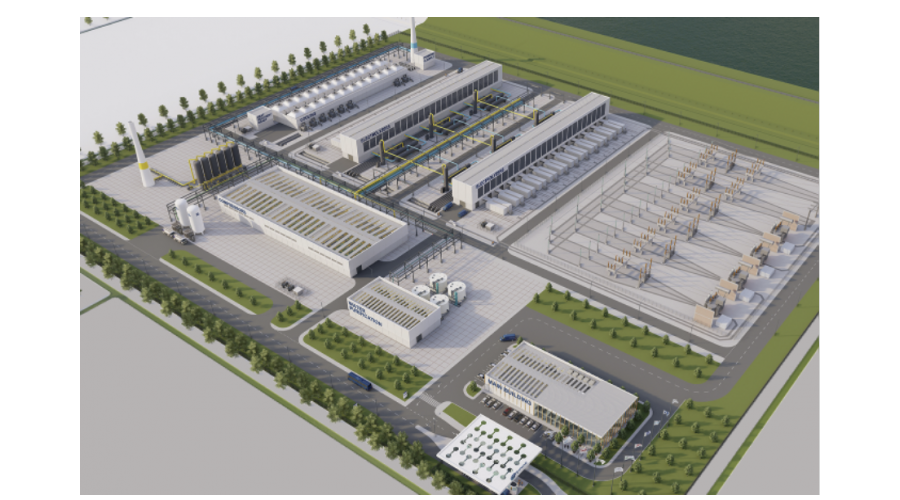
Hydrogen plays an important role in the energy transition as a CO2 and fossil-free energy carrier, feedstock and fuel. But to be able to meet the great energy demand from industry and transport, among other things, we have to produce hydrogen on a huge scale. The current production facilities have a capacity of megawatts, while we need gigawatt installations, and before 2030. The Institute for Sustainable Process Technology presents a design on January 20 for an innovative and advanced green hydrogen plant at gigawatt scale, which can be operational by 2030.
No CO2 is released when green hydrogen is produced by electrolysis with sustainable electricity from, for example, solar or wind energy. Hydrogen therefore plays a key role for the CO2-free (process) industry of the future. Currently mainly as a feedstock for the production of fertilizer, and in the long term also for processes that require a high temperature, such as the production of steel. We currently use coal or natural gas for this.
From megawatts to gigawatts
To meet the energy needs of industry, transport and other sectors, we need to produce enough hydrogen. The Dutch targets for hydrogen in the Climate Agreement include an electrolysis capacity of 3 to 4 gigawatts (GW) in 2030. The European ambition is 40-60 GW in 2030. By way of comparison: the largest existing hydrogen factory now has a capacity of a maximum of 10 megawatts (MW). So we need an enormous upscaling, in 8 years’ time, which is also affordable.
A green hydrogen plant of 1 GW
The Hydrohub Gigawatt Scale Electrolyser project delivered an advanced 2030 design for a green hydrogen plant with a capacity of 1 GW. This plant can use both alkaline water electrolysis (AWE) and polymer electrolyte membrane (PEM) water electrolysis to produce hydrogen. The project of the Institute for Sustainable Process Technology (ISPT) produces a design for a plant that will start in 2030 in a Dutch port area and will run on wind energy from the North Sea. The factory can operate flexibly depending on the amount of wind. In addition, the design complies with grid code and requirements in safety, health and the environment. View in 3D what such a hydrogen plant looks like.
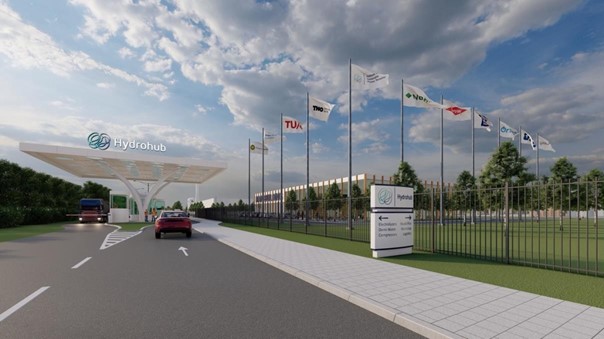
Artist impression of the entrance of a 1 GW green hydrogen plant
Decrease in costs is promising
The blueprint is promising because the investment for an electrolysis plant is manageable. In 2020, the Hydrohub Gigawatt Scale Electrolyser project already delivered a first design for an electrolyser factory. In 2 years time the project has made a better design with the costs almost halved. The expected total investment is now 730 €/kW or 1580 €/(kg H2/d) for AWE and 830 €/kW or 1770 €/(kg H2/d) for PEM. The investment for a GW scale (AWE) electrolysis plant is equivalent to €730 million.
Climate change forces us to accelerate
The goals for 2030 are ambitious. “The Hydrohub Gigawatt Scale Electrolyser project produces a beautiful blueprint. It is now up to industrial parties and knowledge institutes to innovate further. The current results are promising, but we are not there yet. We must work on innovation and realization in order to achieve the goals for 2030. The Netherlands has everything it takes to succeed in this,” explains Carol Xiao, program manager Hydrohub Innovation Program at ISPT. Xiao’s program is already working hard on the necessary innovations in, for example, infrastructure, optimization of electrolyser technology and safety and regulations.
Nienke Homan, board member of GH2 (Green Hydrogen Organisation) and former ‘gedeputeerde Klimaat’ for the Provincie Groningen, is optimistic about the progress towards 2030, but feels the urgency to accelerate. She wrote in the foreword of the project report: “Over the past century we have learned to use oil and gas to create more wealth for everyone. But now we have to make a huge switch and this time we don’t have a century. Climate change is forcing us to act quickly. In fact, we can meet the 2030 deadline – and we will.”
Collaboration by industry and knowledge institutes
In this project, ISPT collaborated with industrial partners Dow Chemical, Gasunie, Nobian, OCI, Ørsted and Yara, and knowledge institutes TNO, Imperial College London, TU/e and Utrecht University.
This project is co-funded by TKI-E&I with the supplementary grant ‘TKI- Toeslag’ for Topconsortia for Knowledge and Innovation (TKI’s) of the Ministry of Economic Affairs and Climate Policy.
About ISPT
As an energetic and open innovation platform for sustainable process technology, the Institute for Sustainable Process Technology (ISPT) connects stakeholders from different sectors and disciplines. We innovate and pioneer to accelerate a more sustainable industry. The industry is an essential player in achieving a circular economy in 2050. It is a driver and
connector in the reuse of residual and waste flows, the integration of electricity demand, the development of hydrogen as a feedstock and energy carrier, and so on. Together we are committed to the transition to a circular and CO2-neutral process industry in 2050. www.ispt.eu
Read the most up to date Fuel Cell and Hydrogen Industry news at FuelCellsWorks