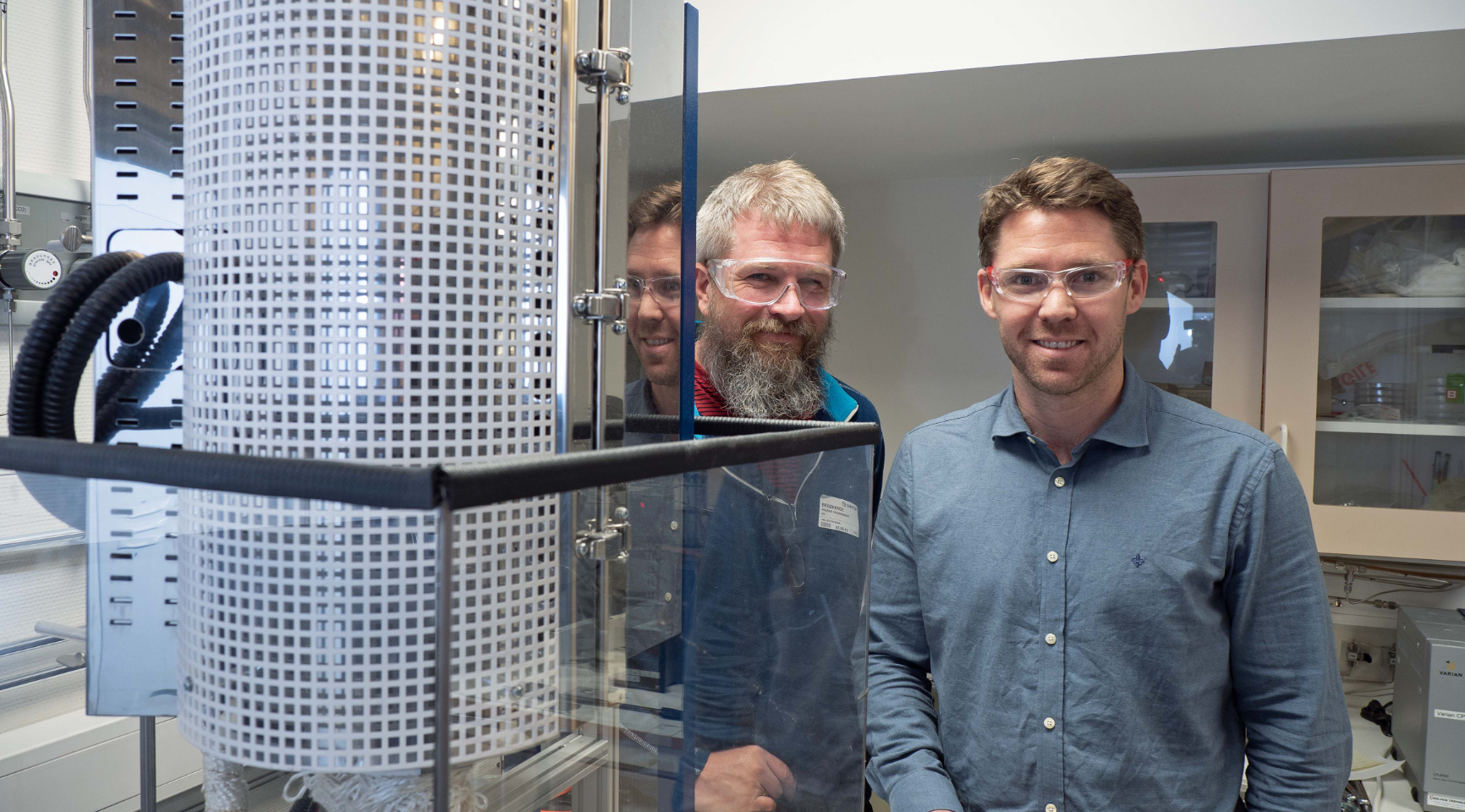
Norwegian scientists have developed the material, which can make hydrogen from water vapor instead of liquid water. It pays off, because heat is cheaper than electricity.
They are the first to make it. The Norwegian-led research group has developed a completely new material that manages to produce hydrogen from water vapor, albeit with high heat and high pressure.
The research results were recently published in Nature Materials: ” Mixed proton and electron-conducting double perovskite anodes for stable and efficient tubular proton ceramic electrolysers ”
Hydrogen stores energy
Hydrogen can take over where the batteries are not holding. When you need to save a lot of energy – more than you need to drive a passenger car for a few hours – it is cheap and good to store it as hydrogen.
– For a long time, very little happened, because it was so cheap to make hydrogen from natural gas and because there was no focus on the climate aspect. Now that we are more concerned with renewable energy, there has been a much stronger focus.
SINTEF researcher Einar Vøllestad.
Very simply explained, you use the energy to split water so that you are left with hydrogen and oxygen. When you then need energy, you turn the whole process around, release hydrogen and regain energy and water.
The dominant way of doing it is still the same as the “water” on Vemork used 100 years ago, explains Einar Vøllestad and Ragnar Strandbakke. Vøllestad is a researcher at SINTEF Industri, Strandbakke is a postdoctoral fellow at the Center for Materials Science and Nanotechnology Chemistry at the University of Oslo.
Low-temperature electrolysis
These are low-temperature electrolysis. The method has become better, cheaper and more efficient. But still, it consumes a lot of energy.
– For a long time, very little happened, because it was so cheap to make hydrogen from natural gas and because there was no focus on the climate aspect. Now that we are more concerned with renewable energy, focus has become much stronger, says Vøllestad.
Renewable energy means that prices fluctuate a lot. There is not as much sun, wind or waves throughout the year. This makes it more important to store the energy from the best production days and use it when the need is greater than the production.
Hot steam helps the reaction
Vøllestad and Strandbakke are working on an EU project where they have researched under completely different temperatures. They use water vapor instead of liquid water to make hydrogen.
– The heat contributes to the reaction. When you get up to temperature, the catalytic activity is much higher, they say. This means that it does not need as much power to get the reaction. Thus hydrogen becomes more competitive. – Heat is much cheaper than electricity, explains Einar Vøllestad.
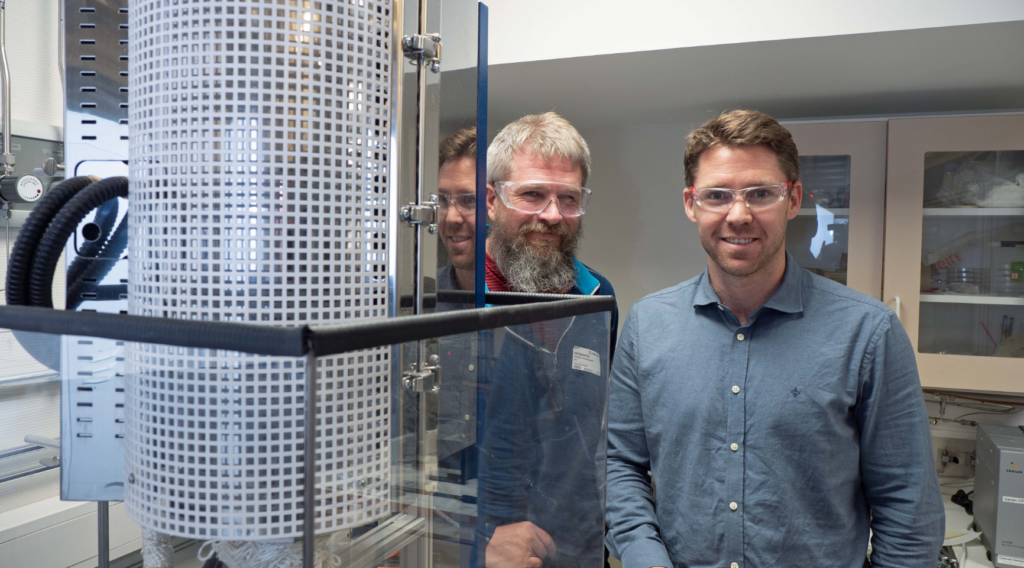
Ragnar Strandbakke (left) and Einar Vøllestad are the first to produce industrial-scale hydrogen with high pressure water vapor. The results were recently published in Nature Materials. Photo: Georg Mathisen.
Facts about the project:
Project Name: GAMER
Duration: 2019-2022 (3 years)
Partners: SINTEF (Norway), University of Oslo (Norway), CoorsTek Membrane Sciences (Norway), Carbon Recycling International (Iceland), CSIC (Spain), MC2 (Spain), Shell Global Solutions (Netherlands)
Funding: 3 MEuro, FCH-JU / Horizon 2020
Website: https://www.sintef.no/gamer/
The forerunner of this project was ELECTRA, funded by the FCH-JU program in FP7
Avoids precious metals
– The fact that you work at higher temperatures also has another advantage. You don’t have to use precious metals.
The next generation of low-temperature electrolysers – that is, the devices in which electrolysis occurs – need platinum and other expensive, precious metals to make water splitting efficient.
– When we go up in temperature and the activity is much higher, we do not need to use the expensive materials to get the reactions, he says.
– It is probably not cheaper to produce such a tube than it is to produce a battery. But you only need one tube where you would need many batteries. Compared to batteries, we have a much smaller consumption of raw materials compared to the amount of energy stored.
– SINTEF researcher Einar Vøllestad.
The problem has been finding materials that can withstand the harsh process when the water vapor holds 600 degrees. This is where the material whites Vøllestad and Strandbakke come in. They began with a list of 120 materials that they thought could do different parts of the job.
– The best materials for this reaction – the ones we thought would be best – do not withstand water vapor at that temperature. We used a material that we knew was good, but saw that it could not withstand the water vapor pressure. So we went in to look at the material and change the chemistry a bit, ”says Vøllestad.
Larger scale
Now they are equipped with the first electrolyzer that is effective on pressurized water vapor and can be scaled and used in industry. It is not enough to do the job manually in a small laboratory – if the research can be used in practice, then the process must be done on a large scale.
– We have made the pipes that are used so that the system is fully scalable. One final advantage is that with this type of technology and this design you get the hydrogen completely dry. In all other electrolysis processes you get hydrogen together with water or other molecules. They must be separated before the hydrogen can be pressurized and stored. It’s not that complicated, but it’s an extra link, and the units are getting bigger, he says.
The material they use consists of barium, lanthanum, gadolinium, cobalt and oxygen. BGLC, as the scientists have christened it.
– What we did was replace some of the barium in the original material with more lanthanum, to simply make it less basic, according to Vøllestad.
Cheaper than battery…
It sounds expensive, but in reality, it will be good economy:
– It is probably not cheaper to produce such a tube than it is to produce a battery. But you only need one tube where you would need a lot of batteries, he explains.
If you imagine a tube and a battery that stores the same amount of power for one hour, the battery will be cheaper. But if you are going to store the same amount of power for 24 hours, then you need to have 24 batteries. If you choose hydrogen, you will still only need one tube. Then you can just fill the tank more and more, and possibly have a slightly larger tank.
– If we compare with batteries, you have a much smaller consumption of raw materials compared to the amount of energy stored, says the SINTEF researcher.
He regards hydrogen as a good alternative, especially in the transport sector and industry. In the transport sector, hydrogen fits when vehicles become heavy and distances long; for trains, ships and trucks. In the industry, Vøllestad brings out the steel mills. There is a lot of heat needed in the production – heat that can then be used to heat the water for electrolysis.
… in the long run
The next step is to make production commercial. CoorsTek Membrane Sciences, which is part of the project as an industrial partner, understands that it will not happen overnight:
– There are long timelines in almost all energy-related technology. It took many years from inventing the lithium-ion battery until we got millions of cars with it, says Per Vestre, who is CoorsTek responsible in Norway.
– We have a long-term perspective on ceramic membranes for electrochemistry. Electrolysis of water vapor is undoubtedly interesting if one manages to mature the technology at the right price. There is no doubt that the market exists, Vestre notes.
Researching the next challenge
– There are still many steps left that need to be optimized and taken further, says Einar Vøllestad. The production method must be upgraded, and stability must be demonstrated over time. We have shown it over 700 hours and measured it on one tube. You need to make a system of a hundred, a thousand, maybe ten thousand pipes for it to be sized.
That job is well underway. The research that has led to BGLC is published in Nature Materials now in June. Publishing in the prestigious magazine takes its time, so the work has progressed well.
– We are a year and a half into a new EU project where we are working to solve the next step with challenges, says Einar Vøllestad and Ragnar Strandbakke.
Source: Sintef
Read the most up to date Fuel Cell and Hydrogen Industry news at FuelCellsWorks