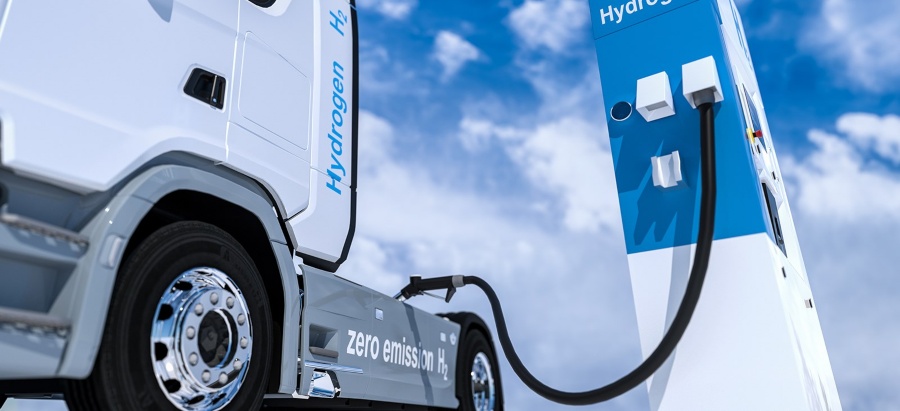
A study about Market for Hydrogen Fuel Cell Trucks shows hydrogen fuel cell technology gives trucks higher range than battery-electric trucks, while offering rapid fueling.
Ramped up to boost H2 fuel cells production
Some industry experts say that hydrogen fuel cells are the future, but others question the technology’s costs and ease of rollout. However, one process that needn’t be expensive is manufacturing pre-coated strip for bipolar plates that are vital in fuel cells. That’s why Sandvik Materials Technology’s (SMT) SurfTech unit has established the world’s first industrial-scale coating line for strip steel used in bipolar plates, with production that is cost-effective and environmentally-friendly.
Fuel cell technology has been around for more than 100 years and was used back in the 1950s and ‘60s in NASA’s Apollo space program. Today, many in the industry are hopeful that hydrogen could be a strong driver towards decarbonization in heavy transport like trucks, shipping and trains because of the technology’s favorable performance. This could hold real advantages for transport systems and, at SMT, we also believe hydrogen can be the fuel of the future.
However, the technology has raised questions. In automotive, for instance, Tesla’s CEO Elon Musk has questioned the technology in comparison with Tesla’s own developments with electric vehicle (EV) batteries. Other large manufacturers oppose, raising benefits and commitment that make you might wonder why there aren’t already more fuel cell electric vehicles (FCEV) on the roads?
Within the transportation industry we already see an accelerated scale up in battery electrical vehicles (BEV). The main limitation for BEV’s is the charging infrastructure (i.e., the electrical grid). At the same time, the infra structure for H2 refueling stations is also limited but much easier to scale up. Thus, the market adoption of fuel cell electrical vehicles (FCEV) will be closely related to the ongoing roll out of hydrogen fueling stations, particularly in Asia, USA and parts of EU, currently at the level of approximately 700 stations and the target of >10.000 stations globally in 2030. This is in turn supported by the green Hydrogen strategies developed within EU as well as many nations. An acceleration into a more complete hydrogen during the coming decade society is in progress.
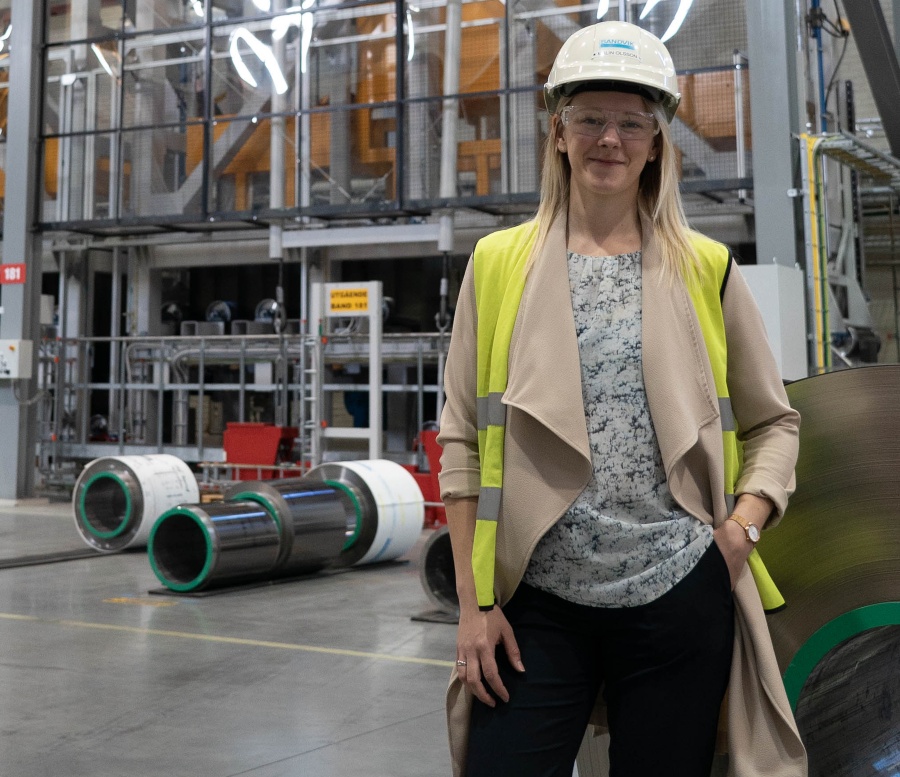
Malin Olsson, Process Development Engineer
“Batteries and fuel cells have been seen as competing technologies. There are advantages and disadvantages with both. Some pros with fuel cells are shorter refuelling time, longer range and smaller size”, explains Malin Olsson, Process Development Engineer at SMT. “The common goal is to decrease the dependency on fossil fuels, andI think that a combination of both battery and fuel cell technology will be vital to successfully reaching that goal.”
With these new technologies, BEV’s and FCEV, there are many new players in the field challenging the big brands like BMW, Volvo, Mercedes etc. For BEV’s Tesla is a well-known company that has challenged the established OEM’s with its vehicles that has been very appealing to the market. Another example is Hyzon, a dedicated fuel cell truck company, is setting up a new plant in Europe for large scale production. Maserfrakt in Sweden has ordered 2 units to be delivered 2022. That is in combination wind a wind powered hydrogen production at their main site.
Excellent electrical properties and corrosion resistance
The environment in the fuel cell is aggressive, and requires materials with good corrosion resistance. Additionally, because the main function of the fuel cell is to produce electricity, it is very important that the bipolar plate is electrically conductive.
To meet the high requirements on the material in the space program, bipolar plates were made of gold, a material that is too pricey for commercial use. So, in order to make fuel cell technology commercial, a material was needed that is cheaper than gold but still with high corrosion resistance and good electrical conductivity. To achieve this, SMT has committed its experience as a developer and producer of advanced stainless steels, special alloys, titanium, and other high-performance materials to develop bipolar plates for fuel cells.
“At SMT, we produce pre-coated strip for fuel cell applications and have developed the Smarter Coatings concept”, says Olsson. “The bulk stainless steel has good formability and stability, while the coatings improve the surface properties, such as lowering the electrical resistance and enhancing the corrosion resistance.“
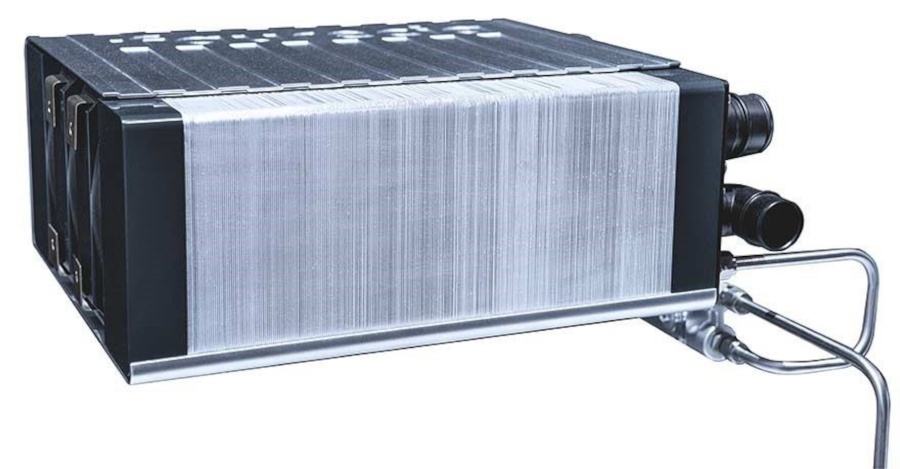
Hydrogen fuel cells are lighter and smaller than lithium-ion batteries, with a greater energy storage density.
The coatings are produced with Physical Vapour Deposition (PVD), a technique used to deposit thin films of one atom, or one molecule, at a time onto a surface with nanometer-level precision. The PVD technique helps ensure a very low content of impurities and foreign elements in the coating and close thickness tolerances of the surface layer.
One product is the Sanergy™ LT pre-coated stainless strip designed for Polymer electrolyte fuel cell (PEFC) applications that are favored for hydrogen-powered vehicles. Sanergy™ LT offers several benefits demonstrated under certain conditions in aggressive environments. They include a good combination of long time proven high corrosion resistance in a PEFC environment and high conductivity. All that with good processing and forming characteristics.
SMT’s pre-coated strip steel portfolio also includes Sanergy™ HT for interconnects in solid oxide fuel cell (SOFC) applications. SOFC runs at a high operation temperature and are typically used in stationary applications. Sanergy™ HT has a low area-specific resistance as well as excellent high-temperature corrosion resistance which ensures low electrical degradation.
Mass production
The development of fuel cells is accelerating worldwide, moving from laboratory-scale and prototype programs to industrial-scale production, which also poses another challenge for manufacturers. As an example, a single hydrogen-powered automobile or bus has between 500 to 600 bipolar plates in a single fuel cell stack. So, if only 1 percent of all cars produced in the world were hydrogen powered, that would require hundreds of millions of bipolar plates being produced each year.
Given all the potential applications for hydrogen fuel cells, mass-production will be an absolute necessity. However, current attitudes to mass-production of fuel cells can be summed-up by the opinion of Herbert Diess, CEO of Volkswagen Group, that the technology in general is “expensive … and difficult to rollout.”
Is it possible to make the production of bipolar plates less costly and more efficient? Yes, explains Olsson: “A common method of producing Bipolar plates is stamping un-coated stainless steel, laser-cut, welding and coating one plate at a time This value chain will be challenged in capacity as it is time consuming, even with high automation level. Our continuous, roll-to-roll PVD coating process is efficient and suitable for big volumes. The pre-coated strip can be directly fed into the customers stamping tools, producing thousands of bipolar plates from each coil. The coating is based on environmentally friendly coating technology that produces bipolar plates made out of 100 percent recyclable material, with no discharge to water or air and no toxic residues.”
Accelerating growth
Processes like SMT SurfTech’s Smarter Coatings concept will be essential for making hydrogen fuel cells commercially viable over the coming years. But, given the debate surrounding fuel cells, how much demand for them will there actually be?
The overall global market for hydrogen fuel cells is expected to grow at a compound annual growth rate (CAGR) of 14.9 percent between 2020 and 2025. Major truck manufacturers in Europe, are calling for the setup of around 300 high-performance hydrogen refueling stations suited for heavy vehicles by 2025, plus another 1,000 hydrogen refueling stations in Europe by no later than 2030.
“As these trends continue, SMT is committed to supporting fuel cell technology and its very important role in the shift towards greener energy,” adds Håkan Holmberg, Sales and Market Manager for Surface Technology at SMT. “As hydrogen fuel cells become used in varied applications including heavy transport, aerospace and more, SMT expects its SurfTech unit to become a key player for producing bipolar plates.”
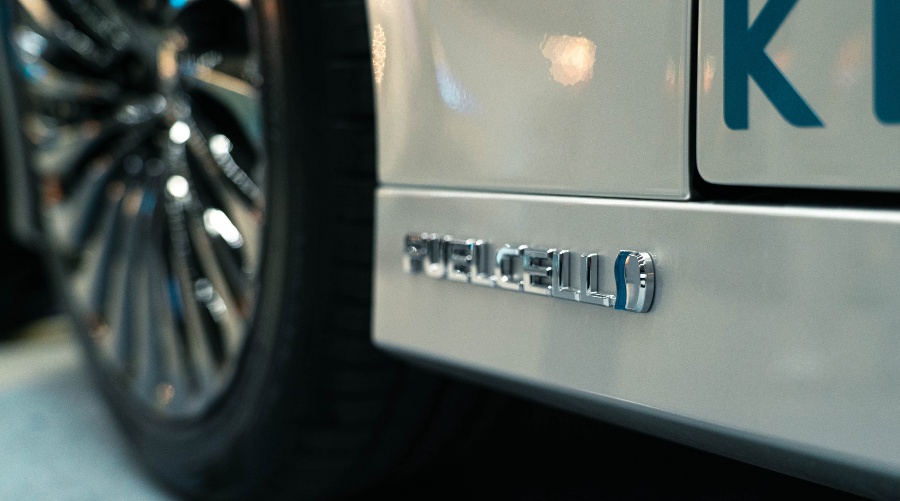
Just over 6,000 fuel cell electric vehicles have been sold and leased in the US, and this figure is expected to grow over the coming years
Read the most up to date Fuel Cell and Hydrogen Industry news at FuelCellsWorks