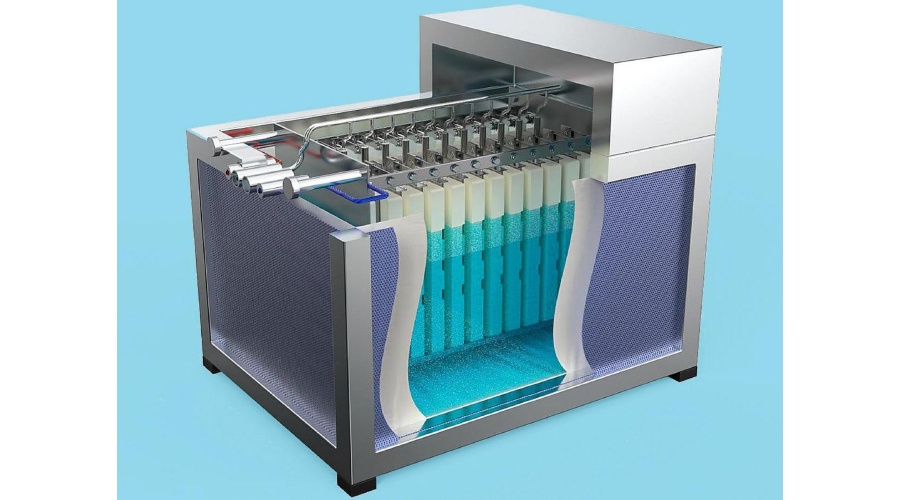
- Tapping the oceans deep for a world of thirsty fuel cells.
Using renewable electricity to split water into hydrogen and oxygen is considered by experts the cleanest route to producing hydrogen fuel. But we live in a world where clean water is a precious commodity to which a third of the world lacks easy access. Researchers in China have now made a device that can directly split seawater to make hydrogen fuel.
The device, reported in the journal Nature, could offer a sustainable, practical route to making hydrogen, its developers say. “[Our] strategy realizes efficient, size-flexible and scalable direct seawater electrolysis in a way similar to freshwater splitting without a notable increase in operation cost,” says Zongping Shao, a chemical engineering professor at Nanjing Tech University in China.
More than 90 percent of hydrogen is currently produced from fossil fuels, leading to a significant amount of carbon dioxide emissions in the process. The oceans and seas could be an endless source of cheap, emissions-free hydrogen. But splitting salty water is difficult with today’s electrolysis devices.
“No extra energy is required to ensure the entry of [pure] water into the system.” — Zongping Shao, Nanjing Tech University.
Electrolyzers have two catalyst-coated electrodes that pass current through water. A membrane separates the hydrogen and oxygen as the gases bubble out of water on each side.
But impurities in seawater can cause side reactions and corrosion, Shao says. Specifically, today’s catalysts convert the chloride ions in seawater to chlorine gas at the anode. Chlorins is an extremely reactive and corrosive gas, and it can degrade the catalysts and electrodes, shortening the lifetime of the device.
Other ions in seawater, such as magnesium and calcium, also react with the catalyst, and form byproducts that can block membranes. Plus, all these side reactions reduce the efficiency of the electrolyzer.
Removing the salts and impurities in seawater is one way to get around the issue, but desalination and purification takes a lot of energy and is expensive. In the past, researchers have also tried to coating the catalysts to prevent these side reactions. That approach has had modest success, Shao says, and is not really practical. Others have made small lab-scale solar-powered electrolysis devices that are membrane-free, but they typically need pumps.
Shao, Heping Xie of Shenzhen University and their colleagues chose to keep the membrane. Instead, they redesigned the electrolysis system in a way that keeps ions and impurities away from the electrodes so that there are no side reactions or corrosion. In their device, two electrodes, separated by a thin film that keeps oxygen and hydrogen apart, are immersed into a concentrated potassium hydroxide electroyte solution.
Porous membranes separate the electrolyte from seawater on each side. The fluorine-rich membrane keeps out liquid water but lets water vapor through.
Now, when electricity is passed through the electrodes, it splits the water in the electrolyte solution. The concentration of the solution increases further, creating a pressure difference between the electrolyte and the seawater on the outside of the membranes. This causes the seawater to spontaneously evaporate, and the water vapor diffuses through the membranes into the electrolyte, where it turns back into liquid water, replenishing the water that was electrolyzed before.
In this way, the electrolysis of water at the electrodes maintains a constant flow of clean water to the electrodes, while keeping out the ions and other impurities in the seawater on the outside of the membrane. “As such, no extra energy is required to ensure the entry of water into the system,” Shao says, “meaning that our electrolyser’s energy consumption is similar to that of an industrial alkaline electrolyser. The cost of the membrane is very low, and it has the preferable anti-fouling performance.”
To show the practicality of the design, the team made a demonstration device containing 11 electrolysis cells. They tested it using real seawater from the Shenzhen Bay. The system worked as intended without failure for more than 130 days, producing 386 liters of hydrogen per hour.
The researchers are now trying to improve the efficiency of the system. They say they could improve performance by trying electrolytes other than potassium hydroxide, and different materials for the electrodes and catalysts.
Read the most up to date Fuel Cell and Hydrogen Industry news at FuelCellsWorks
Shao says that their device could be used to produce hydrogen while simultaneously recovering useful resources such as lithium from water. And it could be extended to applications other than hydrogen production, such as cleaning up industrial wastewater.
SOURCE: IEEE Spectrum