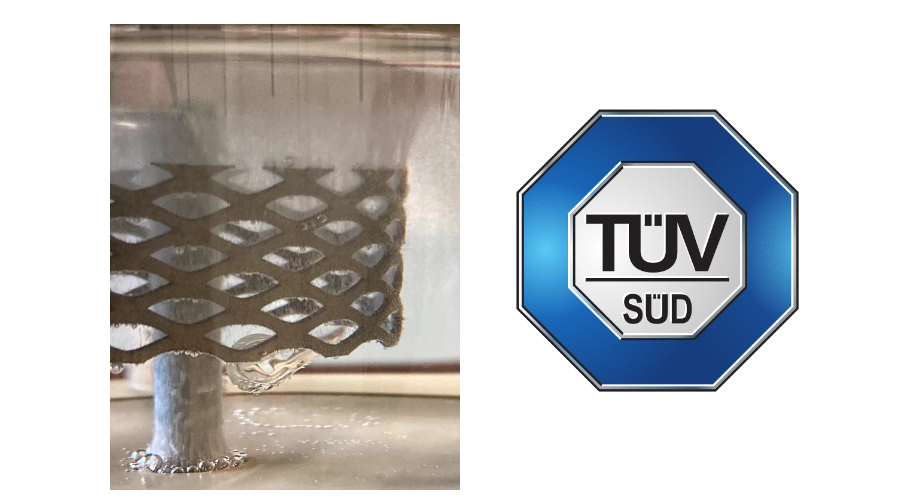
Hydrogen plays a crucial role in the energy transition. The important question here is whether metallic materials in components are suitable for the alternative operating medium. TÜV SÜD tests and certifies materials for their H2 compatibility. For this purpose, materials are charged with hydrogen electrochemically and in gaseous atmospheres.
There are challenges in the transformation to a hydrogen economy at system, component and material level. In stationary and mobile systems, hydrogen can make metallic materials brittle and thus have a major impact on their service life. “Individual tests are often necessary so that components can be operated safely under such conditions,” says Dr. Christopher Tom Engler, materials expert at TÜV SÜD Chemie Service GmbH in Frankfurt am Main.
For the test according to the American standard ANSI-CSA CHMC 1-2014, metallic samples are usually tested in a pressurized atmosphere of H2. However, this is associated with comparatively high costs. “We therefore proceed differently in our state-of-the-art materials laboratory in Kalbach,” says Dr. Engler. “We load the samples with hydrogen, created by electrochemical reactions.”
How the materials react to this is shown by the results of mechanical stress tests and electron microscopic investigations. With this test method, the TÜV SÜD experts create results that are comparable in terms of quality and reliability to the conventional test method involving pressurization, but on significantly more favorable terms.
Another advantage: TÜV SÜD customers not only receive the results of the materials test, but also proof of suitability for H2 compatibility in the form of a corresponding certificate – both from a single source. With this test method, the TÜV SÜD experts create results that are comparable in terms of quality and reliability to the conventional test method involving pressurization, but on significantly more favorable terms.
Operate components and systems safely
In addition to materials, TÜV SÜD also tests and certifies a wide variety of components for their H2 compatibility.
In the hydrogen testing laboratory in Garching near Munich, for example, pressure regulators, sensors, valves, lines and distribution systems are examined in detail.
“We have the necessary equipment and know-how to test the H2 compatibility and safety of components and systems reliably and economically and to issue the relevant certificates if they are suitable,” says Martin Sekura, Hydrogen Business Development Manager at TÜV SÜD Product Service GmbH.
With a global automotive supplier that is a leader in the manufacture of distribution systems (lines and valves) for hydrogen-powered passenger and truck vehicles, a benchmark for the different test methods was carried out as part of a research cooperation.
During this project, TÜV SÜD experts investigated the susceptibility of low-alloy carbon steels as well as high-alloy steels to hydrogen embrittlement in different heat treatment states.
Read the most up to date Fuel Cell and Hydrogen Industry news at FuelCellsWorks
Martin Sekura: “Through this project, our cooperation partner not only receives comprehensive knowledge of the material behavior in its distribution systems, but also proof of the hydrogen compatibility of its products – a clear plus in terms of product safety and transparency.” During this project, TÜV SÜD experts investigated the susceptibility of low-alloy carbon steels as well as high-alloy steels to hydrogen embrittlement in different heat treatment states.